In 2019 Swiss Designer Adrien Rovero, partnered with product development company PCH and SF Design Week with the support of Swissnex, to unveil the installation which features 120 “Shore” modules that are playful inflatable two-sided seats that can easily flip in different directions. Together they create a common gathering space for conversation and community. The Dolos shape was inspired by giant concrete blocks designed in the 1960s by Eric Mowbray Merrifield as seashore erosion protection.
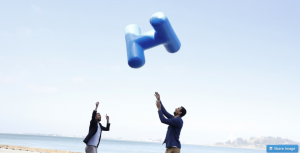
We recently talked to Soft Goods Engineer Jon-William Murphy about the project and how designers can work with engineers and companies like PCH on prototypes for their own projects:
What key requirements drove your approach to realizing Shore?
JWM: Requirements such as: Design intent, the three-month production deadline, allotted budget, and desired quantity – drove our engineering perspective. The use case (the event exhibition with the theme “community”) was also key. The Dolos modules had to be durable, beautifully made, able to be used as furniture and sculpture with safety in mind, easy to set up, and have low environmental impact.
Some of these elements were explicitly required by the San Francisco Design Week (SFDW), some by Adrien, and some were my responsibility to drive.
What is the first question you ask yourself when you see a design specification for a product?
JWM: This project was interesting because Adrien Rovero had several ideas about how Dolos could be made. The key for him was the shape, color, quality and scale of the modules. They are about 4’ tall and wide, and they are an unusual shape/geometry. When approaching any product, the first thing we think about is the different ways it can be made.
Once we evaluate the full range of manufacturing methods that can achieve the form factor, we further filter solutions against the hard requirements. We eliminated the easy ones first. For example, we knew that we could not machine Dolos out of solid billets of aluminum because of budget and timeline constraints. Once we evaluated possible manufacturing methods and materials, we were left with a handful of options. We explored making Dolos from flatpack-style wood, cardboard, and inflatable materials. Each of these options balanced the constraints in different ways (budget, ease-of-installation, timeline). We determined that they could be two-part molded shells of compressed material that attached together to form the modules. Once we settled on what we thought was the best option (inflatable), we began to source material to understand the costs and accessibility (do they have the materials on hand to meet our deadline), and we spoke to a dozen manufacturers to see whether they could meet our deadline, budget, quality, and other requirements.
Does PCH typically engage clients at the concept phase before the design is locked?
JWM: Yes, it is common for us to work closely at the concept phase with industrial designers, other types of designers and clients. We overlap with the design phase at the beginning of projects as well as during the production phase. Working closely with SF Design Week and Adrien was particularly beneficial to executing on this project because of the very tight development, manufacturing and installation schedule (three months). By working closely with Adrien and SFDW and bringing the hard constraints to their attention in real time, they were able to make quick decisions based on what was possible. Part of what we did is give Adrien and SFDW as many good options as possible.
How does getting involved at the concept phase impact the project outcome?
JWM: Getting involved early, working collaboratively, and making quick decisions was the only way to preserve the design intent, otherwise, through the course of the engineering phase, there would have been factors that forced the design to change. If changes are done without consultation and input from the designer, then the project compromises his vision.
What are the key phases in product development that you followed in making Shore?
JWM: The way we break it down is Explore/Architecture/Prototype/Production. This project was no different than the way we approach all our product development. Explore was really about answering: What’s the manufacturing method going to be? Architecture gets into the details of the materials that are possible. Design geometry, and construction asks the questions, How exactly is this going to be made? What are the actual operations? Once we have a sense of how it can be made, we develop a prototype.
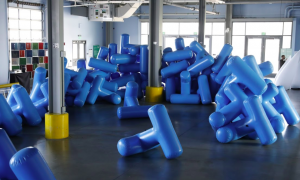
Why did you make a prototype before going to production? What are the benefits and what did you learn?
JWM: Prototyping gave me the confidence that Dolos could be made as an inflatable. Knowing that it is possible, eliminates the possibility that we are giving a potential supplier an impossible task. And because of the unique shape of Dolos – a form that suppliers are likely not familiar with – it is useful to produce a sample to convince suppliers that it’s possible to be made and it helps with their cost estimate. During the build process (creating the prototype), we generally use the proposed manufacturing method for performance reasons. This is not always possible, so in this case, I choose a method of producing a prototype that is more manual but that answers the key question, “Is this geometry reasonably constructed?”
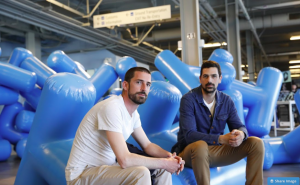
Once the Dolos modules went to production, were you pleased with the first sample? How concerned were you about quality? Did you make adjustments?
JWM: After researching sourcing options with several manufacturers, it took several weeks to find the manufacturer who could meet all our key requirements. We provided our prototype to this manufacturer, who was able to meet our deadline and cost parameters. This manufacturer was also audited for compliance with our sustainability guidelines. Once the factory assured us that they could build Dolos, we ordered a sample, which we could evaluate properly before going to full production. Because of time constraints, I traveled to the manufacturer to evaluate the pre-production samples and decide on any last-minute changes that might be required. As it turned out, there were a handful of details that needed fine-tuning. I communicated with Adrien during this period so that he could give input remotely while keeping the project on schedule.
We know SF Design Week wanted a project that would end sustainably and responsibly after de-install and not create waste for the landfill – how did you come up with this solution?
JWM: Once we decided to go with an inflatable design, we looked for surplus fabric that we could reuse. This included looking at used billboard fabric that was available for resale. After testing, we determined that this fabric couldn’t bond to itself well enough to form an airtight bond. Our second option was to find a fabric that could be recycled and was available quickly. This option was also not possible, so we decided to upcycle the fabric that is used in Dolos. That’s when I found Mafia Bags, a local bag designer and fabricator, who was willing to use the Dolos material to design a tote. The totes, available in orders of 50 or more, retail for $60 each, and can be ordered by contacting maria@sfdesignweek.org
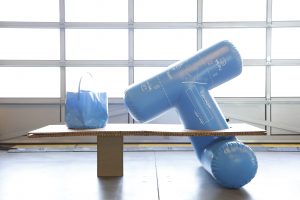
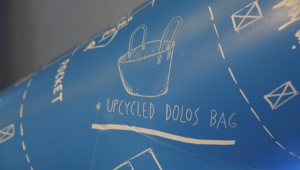
TRAVELING DOLOS
The dolos have been doing a bit of traveling these days. If you have photos from SF Design Week post to Instagram using the tags @SFdesignweek @Adrienroverostudio #PCH #Dolos
About PCH
For more than two decades, PCH has partnered with the world’s leading design-focused brands and innovative startups to create and deliver breakthrough hardware products. Our expertise spans the entire product journey, and we power a unique end-to-end platform that includes engineering and development, manufacturing, fulfillment, supply chain and logistics.
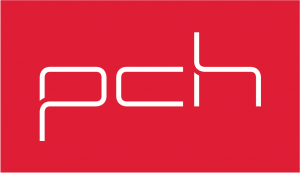